高效智能驱动全局 卓越设备管理软件全新升级
19429202025-03-25下载安装5 浏览
当传统设备管理遇上智能时代,企业该如何破局?
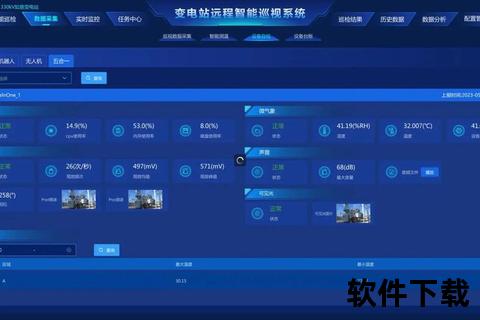
在工业4.0浪潮席卷全球的今天,某大型制造企业曾因设备突发故障导致整条生产线停工3天,直接损失超千万。这不禁让人思考:当设备种类突破5万种、日均产生数据量达到10TB时,传统的人工台账和定期巡检还能否支撑现代企业的运营?高效智能驱动全局的卓越设备管理软件全新升级,正通过三大核心突破给出答案。
1. 设备管理只能依靠人工巡检吗?
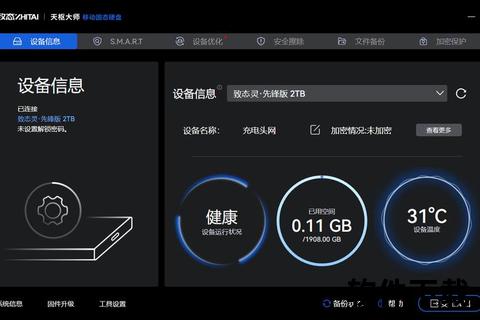
某汽车零部件厂商曾因变速箱检测设备漏检导致批量质量问题,召回成本高达2.3亿元。如今,通过部署高效智能驱动全局的卓越设备管理软件全新升级方案,其设备异常识别准确率提升至99.7%。这套系统搭载的AI预测性维护模块,能通过振动传感器数据提前48小时预警轴承磨损,结合RAG技术调取维修手册和同类故障案例,自动生成包含备件清单的维修方案。
在医疗领域,北京某三甲医院引入的AR智慧巡检系统,使核磁共振设备的年度停机时间从72小时压缩至8小时。维护人员佩戴AR眼镜扫描设备,系统即刻叠加显示设备运行参数、维护记录和3D拆解动画,新手工程师也能快速完成复杂维护。
2. 数据孤岛难题如何破解?
某跨国能源集团曾因设备数据分散在12个系统中,导致海上钻井平台关键部件超期服役引发事故。引入新型设备管理系统后,通过物联网平台整合ERP、MES、SCADA等系统数据,构建起覆盖15万台设备的数字孪生体。系统利用知识图谱技术,将20年积累的维修记录转化为可检索的故障树模型,使平均故障定位时间从4.5小时缩短至17分钟。
纺织机械制造商"华睿源"的案例更具代表性。其零代码开发平台让车间主任也能自主搭建设备监控看板,将原本需要IT部门耗时2周开发的报表生成周期缩短至2小时。系统上线半年,设备利用率提升28%,备件库存周转率提高41%。
3. 成本控制与效率提升能否兼得?
西藏某工程集团在设备管理系统智能化升级中,通过泛普软件的多维数据分析模块,发现22%的挖掘机存在"大马拉小车"现象。系统自动优化设备调度方案后,柴油消耗量降低18%,相当于每年节省1200吨碳排放。更值得关注的是,移动端应用使设备签批流程从3天压缩至2小时,500台特种设备的年检合格率从83%跃升至97%。
在中小型企业领域,"的修工单管理系统"通过二维码+移动端组合,让某连锁餐饮企业的设备报修响应时间从72小时降至4小时。系统自动记录的维修大数据,帮助其淘汰了故障率超标的烤箱型号,年度设备采购预算节省150万元。
智能时代的设备管理行动指南
面对设备管理数字化转型,企业可遵循"三阶推进"策略:首先选择支持模块化扩展的系统,如支持ERP集成的IBM Maximo或灵活定制的Worktile;其次重点突破数据整合能力,优先部署支持5G+边缘计算的物联网模块;最后通过移动端应用实现全员参与,如二维码设备身份证等轻量化工具。高效智能驱动全局的卓越设备管理软件全新升级,正在重新定义"人机协同"的边界——当系统能预测0.01毫米的轴承磨损,或许设备管理的终极形态,就是让故障消失在发生之前。