智能高效极速精准门窗下料自动计算软件一键无忧版
19429202025-03-24app下载4 浏览
<开头部分>
你是否遇到过这样的场景:门窗加工厂里,工人们埋头在图纸上勾画,反复测量、计算,稍不留神就可能因数据误差导致材料浪费?随着定制化需求激增,传统人工下料模式正面临严峻挑战——效率低下、成本高昂、错误频发。据行业统计,仅2023年国内门窗企业因下料误差导致的材料损耗就高达12亿元。在这样的背景下,智能高效极速精准门窗下料自动计算软件一键无忧版(以下简称“一键无忧版”)应运而生,它究竟是颠覆行业的利器,还是昙花一现的概念?
一、传统下料为何耗时费力?
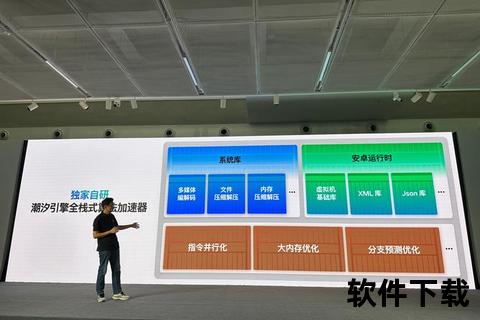
某铝材经销商曾因手工计算错误,导致价值5万元的型材切割报废。负责人回忆:“工人需要同时处理六页窗、双边封等复杂窗型,光是核对公式就占用了60%的工作时间。” 而引入一键无忧版后,系统自动识别窗型参数,3秒生成下料清单。例如,在处理圆头窗的“小太阳”结构时,软件通过弧线算法精准计算切割角度,较人工效率提升20倍。
更值得关注的是其与生产设备的联动能力。广东某智能工厂部署该软件后,通过对接激光切割机与立体料库,实现了从设计到分拣的全流程自动化。2024年数据显示,其日均处理订单量从80单跃升至300单,材料利用率从68%提升至93%。
二、如何破解材料浪费难题?
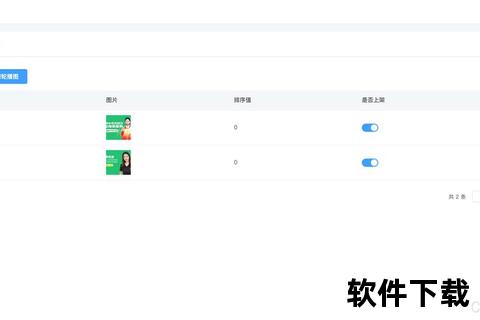
在浙江某门窗企业,软件内置的“型材优化引擎”展现了惊人效果。面对200根长度不一的型材,系统通过智能排样算法将余料控制在3%以内,而传统人工排料的平均损耗率为15%。玻璃优化模块更通过动态规划技术,将异形玻璃(如扇形、多边形)的切割损耗从行业平均的12%降至5%。
典型案例是某工程项目的弧形幕墙加工。工人原需逐块测量156块曲面玻璃,耗时两周仍出现3处尺寸偏差。使用一键无忧版的3D模拟功能后,系统自动生成弧线展开图并同步传输至数控机床,最终实现零误差交付,节省材料成本8万元。
三、非专业人士能否轻松上手?
福建某县城铝材店老板的转型故事颇具代表性。他坦言:“以前请专业设计师月薪要8000元,现在店员培训3天就能用软件完成80%的订单设计。” 这得益于软件的“傻瓜式”操作界面:
输入洞口尺寸后自动匹配图库中的2000+种窗型
拖拽式参数调整,实时显示三维模型与材料清单
扫码枪对接库存系统,自动扣除已用材料
更令人惊喜的是其移动端适配能力。河南某安装队通过手机APP现场测量,实时生成下料单并同步至工厂,使订单响应速度从48小时缩短至4小时。
<结尾部分>
对于不同规模的企业,建议采取差异化应用策略:
1. 小微门店:优先使用基础版,重点突破型材优化与快速报价功能
2. 中型厂商:搭配立体料库与自动分拣系统,构建柔性生产线
3. 大型集团:整合ERP与MES系统,实现全产业链数字化
智能高效极速精准门窗下料自动计算软件一键无忧版的价值,不仅在于替代人工计算,更在于重构了“设计-生产-交付”的产业逻辑。当行业平均交付周期从15天压缩至3天,当每吨型材多创造2000元效益,这场由算法驱动的效率革命,正在重新定义门窗制造的边界。